Plastic or metal? When peace of mind must be top priority
At the design stage of any product, there’s a lot to think about in terms of the materials you might use. Different materials offer different properties and it’s important to weigh up the key attributes and match them to the needs of the application. Regardless of the end product - a toy, a cake, an electronic device - characteristics such as aesthetics, longevity, weight, colour, strength, cost… these and so many more will need to be carefully considered to ensure the best outcome and a product that’s fit-for-purpose.
One vitally important characteristic of any item, whatever its intended purpose, is one that upholds the safety of the consumer.
There’s no question about it, when it comes to public safety, there can be no compromise.
Whilst enforced by law through health and safety legislation, there is also a moral obligation to take care of people’s well-being and to value their safety as a primary concern.
Let’s consider the properties of two primary materials used in display electronics and ask, for specific elements of construction, would you choose plastic or metal?
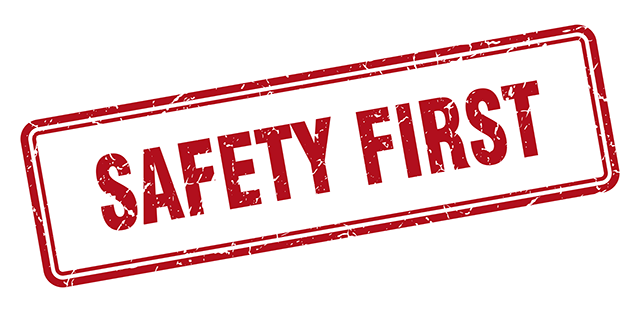
Fire-retardancy – hindering the spread of fire
Protection from fire in public spaces has significant implications for the selection of materials. The construction of buildings must by law integrate fire-retardant elements designed to limit the spread of fire and give more time for people to escape.
In 2019, Brussels Airport launched a tender that described LCD and LED based video wall products as “cladding”. For manufacturers of electronic equipment this has significant consequences as their products now require the same fire classification as construction materials. The fire load test measures a product’s reaction to fire including its contribution to the spread and intensity of flame and the release of smoke and burning droplets.
In order to pass this test, the use of materials within electronic equipment will be of paramount concern and an understanding of the property of certain materials will be fundamental to its design.
- As a non-combustible material, metal is highly heat resistant with a very high melting point, slowing its degradation under extreme high temperatures.
- Plastics, in contrast, are highly combustible. Burning plastic releases dangerous chemicals and drips as it burns.
Naturally enough, being easy to fabricate, plastic in one form or another will be needed for certain components, but when it comes to the chassis or framework upon which the device is built, likely to be a large expanse and the greatest proportion, the choice of material will be fundamental. What would you choose, plastic or metal?
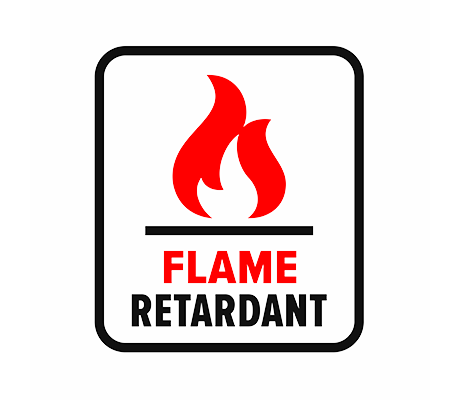
An LED product built using a plastic chassis would NOT pass the fire load test. There are ways around it, by investing in an array of structural or plant-related compensation such as sprinklers and smoke evacuation systems. It is an additional costly investment, but more to the point, when it comes to peace of mind, would you choose plastic or metal?
Heat resistance – maintaining long-life, fit-for-purpose performance
Whilst it is hoped that a product’s fire-retardant properties will never have to be put to the test in real-life, heat remains a challenge for electronic equipment every day that its operational.
Heat is no friend to electronic devices. Managing heat build-up and maintaining a constant temperature is a concern for manufacturers and operators. Not only does it impact on the lifetime of the device and the consistency of its performance, it is vital in guarding against combustion.
- Metal is an excellent conductor of heat. As such, it is highly efficient at dissipating heat, expelling it away from the internal workings of the device.
- Plastics are thermal insulators, high temperatures are trapped inside the device, building up over time.
If you want to protect your investment and extend the life of your device, which material would you like to see specified for the chassis, plastic or metal?
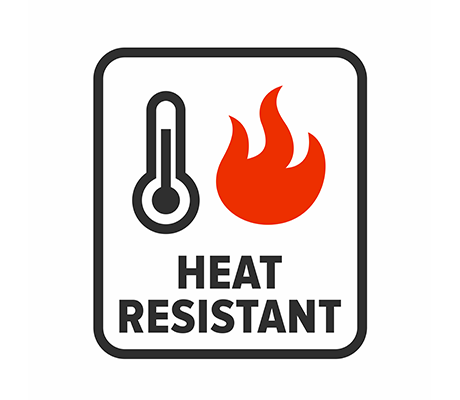
Precision – ensuring perfect alignment
Exactness of alignment is fundamental to creating overall visual impact, after all, who wants to see gaps between the modules on an LED wall? Heat is a major contributing factor as it directly impacts the integrity of the cabinets which support the LED pixel cards.
- Metal is precisely machined to size. It is strong, rigid and durable even in changing temperatures.
- Plastic is pliant. It will expand and contract when subject to changing temperatures.
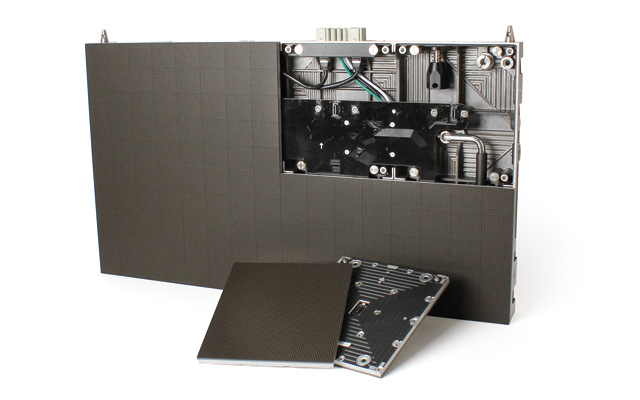
When you have invested in the latest technology you want it to look sleek and seamless, in perfect alignment and uniformity, creating the impression of a single vast canvas. You want your audience to say WOW! Which material says wow to you, plastic or metal?
Recyclability – being environmentally responsible
The recyclability of a product will have implications not only for the environment but also for the reputation of your business. Organisations must act responsibly towards the environment to meet the expectations of business stakeholders and society in general.
- Metal is 100% recyclable. It can be recycled again and again without altering its properties.
- Not all plastics are recyclable. Because of the way plastic is fabricated, it is not always possible to be returned to its original constituent elements.
When you’re quantifying your carbon footprint, which material usage are you most confident to declare, plastic or metal?
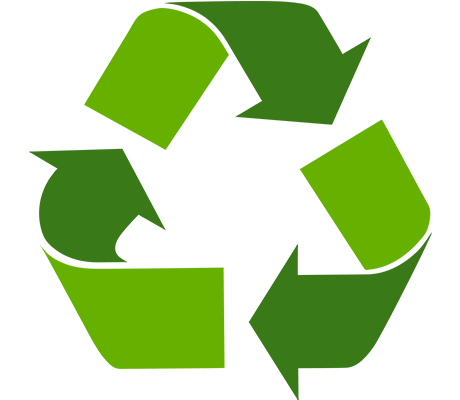
So, what’s it to be, plastic or metal?
The question is not a simple case of cost over quality, it is a matter of fit-for-purpose design at a reasonable cost. That question alone makes the choice between plastic or metal a far more straightforward outcome. Surely the question itself is far simpler. Why plastic?
Find out more in our whitepaper: